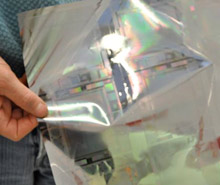 |
Print out: This plastic material is used as the backing for Phicot's amorphous silicon electronics.
Credit: Phicot |
Engineers and technophiles have long dreamt of plastic-based displays that are flexible, lightweight, and rugged compared to their glass-backed counterparts. But plastic screens still aren't widely available, partly because they're so hard to manufacture reliably in large numbers.
Now a company called Phicot has adapted a technique for printing amorphous silicon electronics onto plastic that could finally make such displays practical. The manufacturing technique, already used to make cheap solar cells, involves depositing chemicals on long sheets of plastic as they are fed through a series of rollers. Phicot is a subsidiary of PowerFilm of Ames, IA, which already makes amorphous silicon solar cells using this roll-to-roll process.
"The basic technology of roll-to-roll can bring the price down and make plastic an excellent option for the back half of the display," says Frank Jeffrey, cofounder and CEO of PowerFilm.
Most modern displays rely on transistors made of polysilicon--a semiconductor that allows electrons to move fast enough for video. The problem with polysilicon is that it needs to be deposited at high temperatures that melt plastic. So Phicot turned to amorphous silicon, which can be deposited at low temperatures and yet is still fast enough to control the pixels of electrophoretic displays such as E-Ink, and eventually those in an organic light-emitting diode (OLED) display.
At Phicot's facility, layers of amorphous silicon and insulating materials are deposited onto plastic. These rolls of plastic are then sent to a facility at HP Labs, where engineers use a novel kind of lithography, called self-aligned imprint lithography (SAIL), to etch transistors onto the plastic's surface.
Once the transistors have been deposited, the screen itself must be added. HP has tested its transistors using E-Ink and with its own reflective display technology, capable of showing color and video. According to Carl Taussig, director of HP's information surfaces labs, the amorphous silicon transistors could, with slight changes to their chemical makeup, also drive OLEDs.
Phicot isn't the only company trying to make plastic-based displays. Polymer Vision, a spin-off of Philips, and Plastic Logic are both promising products in the near future. However, these devices will rely on transistors made of organic materials, which are easy to deposit on plastic at low temperatures, but operate more slowly than those made of amorphous silicon. While organic transistors are good enough to power electrophoretic displays, they are incompatible with OLEDs. Another company, Kovio, is aiming to print silicon on plastic using technology that resembles an ink-jet printer; the main applications at this point are RFID tags.
Another advantage of amorphous silicon over organic materials is that its electronic performance is well known. "Organics are less well developed," says John Rogers, professor of materials science at the University of Illinois, Urbana-Champaign. "[Organic components] have uncertain stability and limited long-term reliability; they also have not been used in large-scale applications."
The transition from thin-film solar to printing display transistors was relatively simple, says PowerFilm's Jeffrey. The major difference is that the layers are deposited in a different order. Some layers also need to be doped--adding impurities to change a layer's electrical properties--in a different way. "We used our solar-cell machines to do the first development work," he says. "It was very straightforward."
Phicot is planning to move to a facility in Silicon Valley by the end of the year to take HP's SAIL technology to a large space.
But the process is far from perfect. Jeffrey says that the engineers are quickly solving many of the defect challenges--the major obstacle to mass production at this point. For instance, the process must be fine-tuned so that the plastic isn't stressed in a way that could, down the line, result in defective circuitry.
Another challenge is making sure that the plastic is as defect-free as possible to start with. "Your plastic has to be smooth," says Alberto Salleo, professor of materials science and engineering at Stanford. "And as it goes through the rolls it shouldn't expand or crack."
Jeffrey says there may be ways to adapt the electronics to flaws in the plastic. "We have a possible option of designing our circuitry to tolerate those" he says.
Copyright Technology Review 2010.